Dual-Purpose Systems for Better Food Safety and Efficiency
Food safety and accuracy are top priorities for any food manufacturer. Weighers ensure products meet weight requirements, and metal detectors help prevent contamination. Dual-purpose systems that combine these functions are now available, providing a more effective solution for quality control. This article will explore how these combined systems change food processing plants' operations, ensuring safer, more reliable products.
The Role of Checkweighers in Food Processing
Checkweighers are automated systems ensuring each packaged product meets specific weight requirements. They weigh individual items as they move along the production line to ensure they are within the acceptable weight range. If a package is too light or heavy, the system automatically rejects it to prevent non-compliant products from reaching consumers.
-
Compliance and Quality Assurance
In Australia, laws like the Australian Consumer Law (ACL) ensure that products are labelled accurately. It means providing the correct weights, as regulated by the Australian National Measurement Institute, to give consumers accurate information about the products they buy.
Checkweighers are essential in the food and beverage industry. They ensure that packaged products meet the specified weight. This helps manufacturers follow packaging laws, reduce waste, and maintain consistent product quality. Checkweighers also help find problems with filling systems and identify product imperfections or packaging damage.
-
Process Efficiency and Product Safety
Checkweighers help make processes more predictable by confirming ingredient batch weights and measuring pre-cooked weight to prevent variations in heat processing, ensuring the final product's quality and safety.
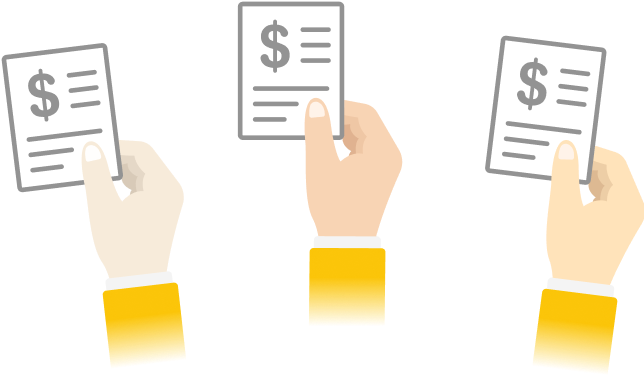
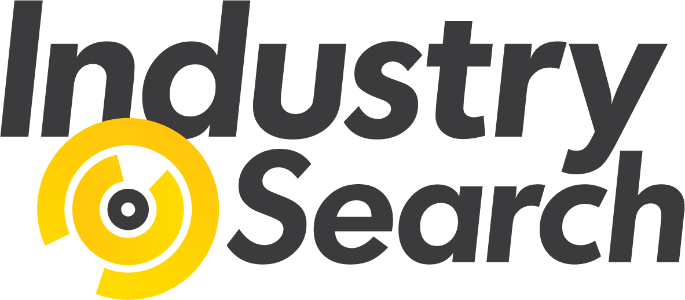
Find the right Checkweigher
Compare quotes from expert Australian suppliers and make the best choice. It's free, quick and easy!
The Importance of Metal Detection in Food Processing
Metal detectors are essential for food safety. They prevent harmful metal pieces from contaminating food. Detection systems also help find and remove contaminated products before they are sold, ensuring consumer safety
-
Detecting Microparticles for Food Safety
Metal detectors are crucial for detecting small metal contaminants in food that are invisible to the human eye. These contaminants come from processing equipment and can be harmful if consumed. Finding these bits before the food is sold helps keep people safe and stops companies from having to take back their products.
- Preventing Equipment Breakdowns
Detecting high levels of metal contamination in production equipment can indicate potential issues. Finding these fragments early allows for preventive maintenance before a machine breaks down during production and helps maintain production line efficiency before it becomes a significant problem.
-
Saving Time and Costs in Quality Assurance
Metal detection significantly improves the quality assurance process by reducing the need for manual checks. Low-maintenance, automated metal detection systems can run continuously with minimal oversight, allowing workers to focus on more complex tasks. This automation enhances efficiency and saves valuable time.
Advantages of Dual-Purpose Systems
Dual-purpose systems that combine check weighing and metal detection offer several critical advantages for food processing plants:
-
Optimising Operations
Combining check weighing and metal detection in one system simplifies food production. With fewer machines to operate and maintain, manufacturers can simplify their workflow, reducing complexity and improving overall efficiency.
-
Space and Cost Reduction
Dual-purpose systems help save costs by combining two machines, lowering purchase and maintenance expenses. Additionally, the compact design frees up valuable space on the production floor, enabling better use of available resources.
-
Real-Time Alerts and Faster Adjustments
These systems provide immediate feedback on weight and contamination issues. Real-time monitoring detects problems instantly, allowing manufacturers to adjust and maintain optimal production speed quickly.
-
Accuracy and Consistency
Manufacturers benefit from checking weigher accuracy by integrating weight and metal detection into one system. This results in consistent product quality, reduced waste, prevented recalls, and ensured that all products meet regulatory standards.
Key Features of Dual-Purpose Systems
Dual-purpose systems in manufacturing improve efficiency and accuracy, allowing quick switching between different products.
-
Multilingual Interface: Easy for operators of all languages to use, reducing training and errors.
-
Heavy-Duty Build: Durable for long-term use in harsh environments.
-
USB Data Port & Storage: This makes data transfer and backups easy while storing essential production data.
-
Password Protection: Limits authorised users' access to sensitive data and settings.
-
Automated Rejection: Quickly removes faulty products, improving quality control and reducing manual checks.
-
Auto-Learn Programming: Simplifies setup for new products, ensuring accurate processing.
-
Touch Screen & Internet: Offers real-time data through an easy interface with remote monitoring capabilities.
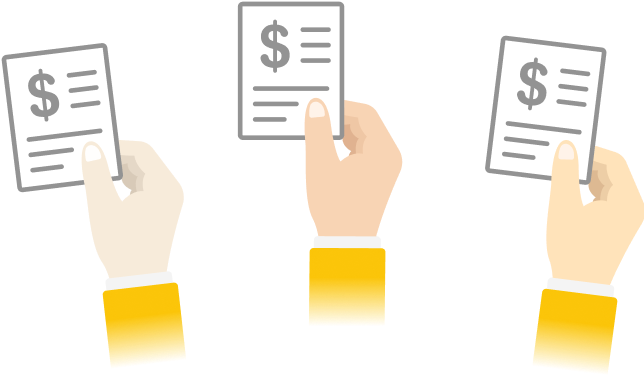
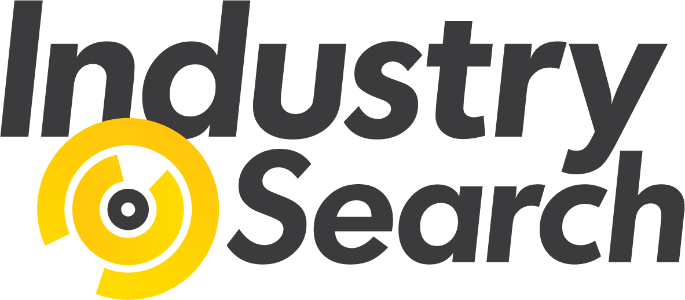
Find the right Checkweigher
Compare quotes from expert Australian suppliers and make the best choice. It's free, quick and easy!
Applications in the Food Industry
Dual-purpose systems that combine check weighing and metal detection are essential in various food processing sectors. Here’s how they are applied:
-
Meat Processing
In meat processing, these systems ensure that packaged meats meet weight requirements and are free from metal contaminants, maintaining safety and compliance with regulations while optimising portion sizes and reducing waste.
-
Dairy Products
Dual-purpose systems verify weights and detect metal particles introduced during manufacturing to ensure product safety and high quality while streamlining production processes for dairy products like cheese, yoghurt, and milk.
-
Bakery Goods
In bakeries, these systems check the weights of bread and pastries to avoid over or underfilling. They also detect metal contamination from machinery, helping to maintain product quality and consumer safety.
-
Packaged Goods
In the packaging sector, dual-purpose systems ensure all packaged foods meet weight specifications and are free from contaminants, increasing efficiency, reducing waste, and enhancing product integrity.
-
Snack Food Manufacturing
These systems help ensure proper weight and detect metal objects for snack foods like chips and pretzels. By integrating both functions, manufacturers manage operations and improve safety, building consumer trust.
Considerations When Choosing a Dual-Purpose System
When selecting a dual-purpose system for check weighing and metal detection, several important factors should be considered to ensure optimal performance and compliance in your food processing operations:
-
Sensitivity of Metal Detection
Choose a system with adjustable sensitivity settings for different product types and packaging materials. This flexibility helps detect even small metal fragments, maintaining product safety.
-
Weight Range
Consider the check weigher's weight range, which should match the typical weights of the products being processed. Ensure that the system can accurately measure the full range of weights in the production line to avoid under or overfilling and maintain compliance with regulations and customer expectations.
-
Line Speed Compatibility
Evaluate the dual-purpose system's compatibility with your production line's speed. The system should operate efficiently at the required line speed without causing delays. Check the maximum rates to ensure the system can meet production demands.
-
Maintenance and Calibration Needs
Consider the dual-purpose system's maintenance and calibration requirements. Look for systems with user-friendly calibration processes and minimal maintenance to reduce downtime and operational costs.
Conclusion
Dual-purpose systems that combine check weighers and metal detectors improve food safety and efficiency. They help ensure products meet weight and safety standards, reduce waste, and make compliance easier. These systems allow manufacturers to produce safer, higher-quality food for consumers.
In Need of a Checkweigher?
Ensure your packaged products meet industry standards. Reach out today for a quote designed to suit your specific requirements! Request a checkweigher quote today!
FAQ:
-
What is a dual-purpose system in food processing?
A dual-purpose system combines both check weighing and metal detection functions into one machine. These systems ensure products meet weight requirements while detecting and removing any metal contaminants from the production line. -
How do checkweighers improve food safety and quality?
Checkweighers ensure each product meets the specified weight requirements, helping manufacturers comply with packaging laws, reduce waste, and maintain consistent product quality. -
Why is metal detection important in food processing?
Metal detectors prevent harmful metal pieces, which may come from processing equipment, from contaminating food. This helps ensure consumer safety and reduces the risk of product recalls due to contamination.